How Did VISEO and Anaplan transform inventory management for an american lingerie retailer?
Established in 1935 in Kuala Lumpur, Malaysia, our client has grown into Southeast Asia’s premier luxury goods and 360° retail specialist, operating over 350 stores across the region. With a diverse portfolio of over 200 brands, they span categories such as fashion and accessories, timepieces and jewelry, perfume and cosmetics, as well as confectionery and dining concepts. In 2022, our client, embarked on a six-month project to implement solutions for one of their key brands, a renowned American luxury lingerie, clothing, and beauty retailer with 88 stores across 7 countries.
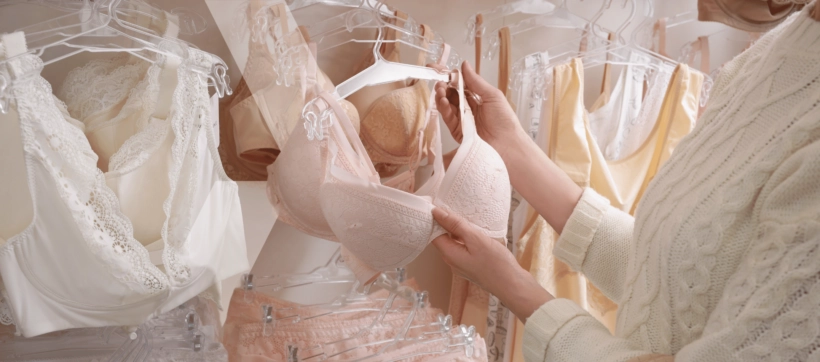
The Challenge
The client faced several operational challenges. Their team relied on manual allocation and replenishment processes for more than 8,000 SKUs across 88 stores. This method consumed time and resources. Specifically, six allocators spent more than three days generating delivery notes using the ERP system. In addition, they lacked formal Standard Operating Procedures (SOPs) and Key Performance Indicators (KPIs), making it difficult to track performance. The stores often faced overbuying and large stockpiles, leading to frequent store-to-store transfers, which increased inefficiencies and costs.
The Solution
To solve these issues, VISEO collaborated closely with the client’s business team from the start. This approach helped ensure alignment throughout the project. Over two months, the team conducted a thorough discovery phase to map out the client’s needs and develop clear procedures. VISEO employed Agile methodology, implementing the project over three sprints of three weeks each. This method allowed for continuous feedback and improvements during the build and deployment phases.
VISEO also automated delivery note creation and integrated the process with the ERP system, significantly reducing manual labor. The introduction of new inventory KPIs enabled real-time tracking and monitoring of stock levels. This automation reduced the reliance on store-to-store transfers, improving efficiency across the entire network.
Achievements Unveiled
The project’s success can be largely attributed to the early involvement and commitment of the client’s business team. Key achievements included:
- Strong business team involvement from the discovery phase to the deployment phase, which fostered quick adoption and efficient use of the new systems.
- Key users from the client’s side played a pivotal role in ensuring that the solution met operational needs, making the implementation process smoother and more effective.
- Several enhancements were made during the User Acceptance Testing (UAT) and hypercare phases, ensuring that the solution was tailored precisely to the client’s evolving needs.
The Outcome
The implementation resulted in significant improvements across the board, particularly in time efficiency and inventory management:
- The time required for the allocation process dropped from three days to just three hours, dramatically increasing operational efficiency.
- The delivery note creation process was fully automated and integrated with the ERP, saving labor hours and reducing errors.
- Inventory KPIs were implemented and monitored, providing real-time data for decision-making.
- Store-to-store transfers were reduced significantly, leading to more efficient inventory distribution and lower overall costs.
With the strong support of key sponsors and involvement of both business and IT teams, the project not only streamlined operations for this American luxury lingerie retailer but also set a strong foundation for expanding these solutions to other brands within the group in the future.
Transform how you plan your business with Anaplan in Asia
See in real time, plan for the future, lead with confidence. Ready to achieve outstanding results and exceptional customer experiences with VISEO and Anaplan?
By bringing together VISEO’s comprehensive industry insights and technology experience with Anaplan’s advanced capabilities, we can make our clients’ digital strategy a reality, allowing them to be more productive, innovative, and competitive.